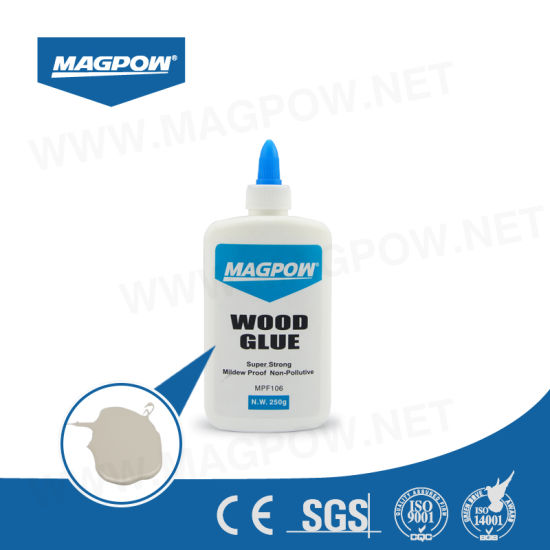
It can be difficult to transport rough lumber in your car. You should always bring your hand saw, tape measure and other tools with you to the store. Also, make sure to buy extra boards in the event that the one you have purchased doesn't fit. Also, be sure to purchase the board with checks and knots, as they may not get planed down as you expect. You don't want the board to be ripped and you have to start over. This is a wasteful way to spend your time and money.
Minimal wastage
A sawmill usually turns 59% of rough lumber into boards when cutting it. The rest of a log is usually waste: sawdust chips, bark and chips. While a less-than perfect cut will result in more waste it should still be below 20%. Here's how to estimate the amount wasted wood in a board. For a nominal 4-foot board, the sawmill should remove about 18% of its volume to achieve the desired lumber thickness and width.
For one, rough lumber doesn't come in uniform sizes. The dimensions of hardwood bought from a big box store are often known, allowing you to plan your project around the standard size. The rough edges of lumber can be uneven, which leads to wasted material. The common width of rough-cut lumber can lead to a lot waste. This waste cannot be reused later.
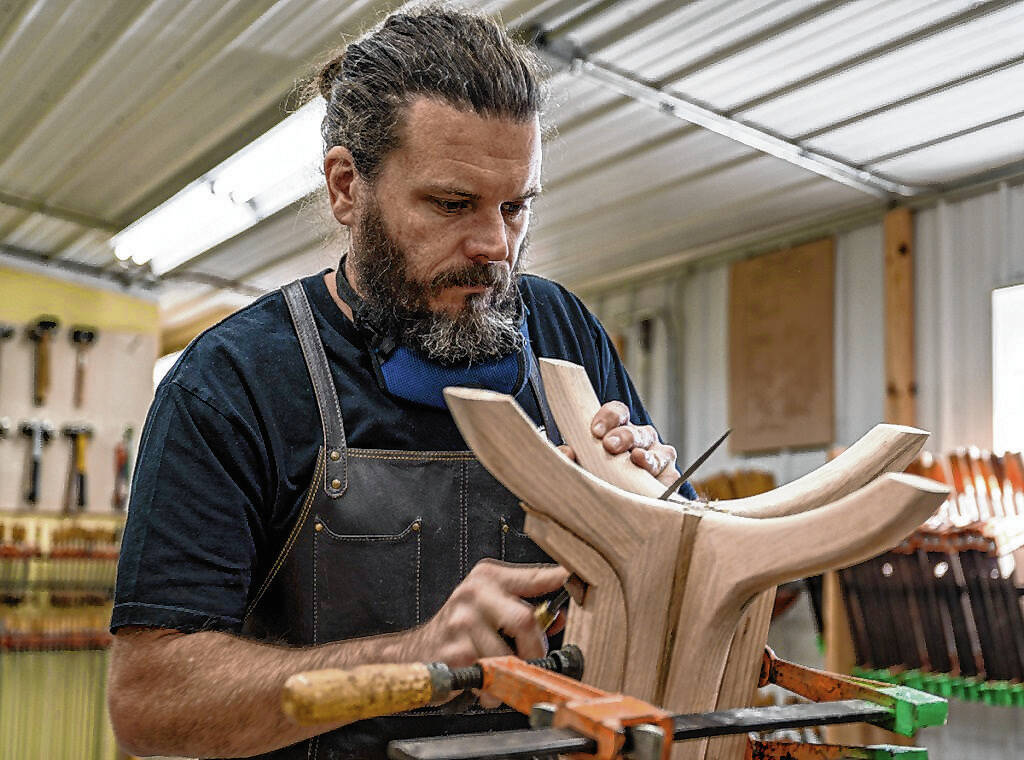
Preparation
Before you begin to cut rough lumber, measure its length. The lumber yard may not have the rough lumber perfectly flat upon arrival. It may not be perfectly flat and have uneven edges and faces. Therefore, it may take multiple passes to flatten. The rule of thumb is 1/16" per pass. If the lumber has concave edges, you can run it through a saw with the concave side down.
In general, rough cut lumber should not be more than 1/4" thick before the saw cuts. After flattening your face, plane the board to the desired thickness. Measure the length and width of the finished lumber once you have determined the thickness. You should account for any imperfections. Make sure to leave at least one-quarter inch of space between each board. Plan your project around the available boards. Hard to work with lumber that is too warped, bowed or twisted.
Cost
There are two types, dimensional lumber and rough sawn lumber. Home improvement shops usually sell finished lumber but only rarely rough-sawn. Both types of lumber are typically carried by local sawmills or lumber yards. There is a difference in how much work it takes to process the two types. Because it takes less work to make, rough-sawn boards are more affordable. It is also smaller and lighter than finished lumber.
While buying lumber from a yard or mill is cheaper, you are less likely than others to find it in standard lengths. Although milling your own lumber is cheaper than buying rough-sawn lumber it can still be an economical option. However, you will need to have enough shop space and more power. It can also be noisy and requires some training. Zoning laws may be necessary if your mill is to be used in an area.
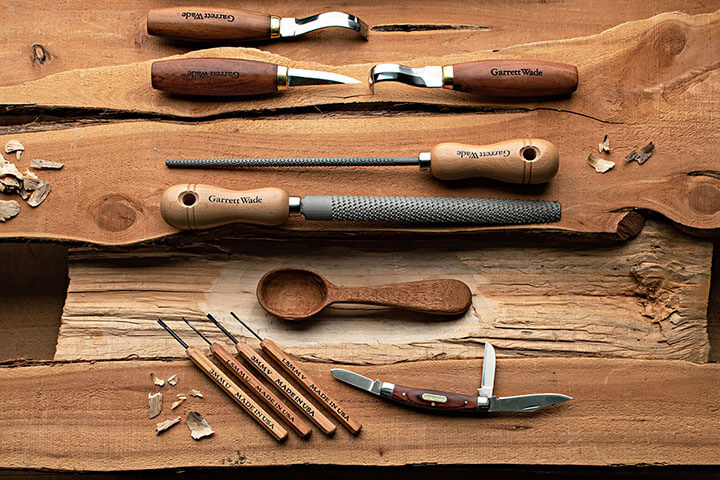
Source
There are many options available when you buy lumber. There are many sizes and shapes to choose from, as well as different finishes. Rough sawn lumber can be described as unfinished and unsanded lumber that is not cut into planks. This type of lumber is more durable than others because it contains more moisture. It's also thicker and stronger than surfaced wood. These are some of many advantages to rough sawn lumber in your woodworking projects.
First, it is affordable and readily available. Rough lumber is not treated and is not usually sold at a hardware store. This lumber is not treated and has some pros and cons. This lumber is cheaper per board foot but less expensive by volume. It takes longer to finish than treated wood. When deciding how many lumber to buy, this is an option you may want to consider. If you plan on using rough sawn lumber for your project, consider purchasing a large quantity of it and a small amount for finishing.
FAQ
How much money will I need to get started?
Since every project differs, it is impossible to give exact numbers. These factors will help you get an estimate of how much money is needed.
-
Materials cost
-
Tools and equipment
-
Time spent on the Project
-
Hourly rate
-
What amount of profit can you expect to make?
-
Hire help
It's a good idea for beginners to start with small projects like frames and boxes. You will gain more experience and be able to tackle larger projects.
What tools work best for me?
It helps to reflect on your needs and preferences before you shop for tools. Do you prefer metal handles or plastic? What size are you most comfortable using for screws and nails? Do you prefer hand tools over power tools?
Are you looking for tips to start a woodworking company?
It can be difficult to start a woodworking shop. It's worth it if you're passionate and willing to work hard. You'll enjoy the challenge and rewards of owning your own business.
It is important to remember that unexpected problems may arise when you start a new venture. For instance, you might run out of money unexpectedly. You might find customers not willing to pay the amount you expected. Preparedness is key to survival in such situations.
One tip is to have a separate banking account for your company. You'll be able to track how much money comes in and out.
How much money does a hobbyist have to put into getting started?
If you're looking to start your own woodworking business, you'll probably need some capital to buy the necessary tools and supplies. You can start by purchasing a small table saw and drill press as well as a circular saw, circular saw, jigsaw and sanding machines. These items don't cost much so they won't break your budget.
Statistics
- Average lumber prices rose about 600 percent between April 2020 and May 2021. (familyhandyman.com)
- The best-paid 10 percent make $76,000, while the lowest-paid 10 percent make $34,000. (zippia.com)
- If your lumber isn't as dry as you would like when you purchase it (over 22% in Glen Huey's opinion…probably over 10-15% in my opinion), then it's a good idea to let it acclimate to your workshop for a couple of weeks. (woodandshop.com)
- Woodworkers on the lower end of that spectrum, the bottom 10% to be exact, make roughly $24,000 a year, while the top 10% makes $108,000. (zippia.com)
External Links
How To
How to join hardwood without using nails
Woodworking is a favorite hobby. Woodworking can be a fun hobby because you can work with your hands to make useful objects from wood. You may need to join two pieces without the use of nails. This article will help you to maintain the beauty of your woodwork projects.
First, remove any sharp edges from the wood pieces before you join them. Do not leave any sharp corners as they could cause problems down in the future. Once you have done that, you can begin gluing your boards together.
When working with hardwood, glue should be applied only to one side. If you're using softwoods like pine or cedar, you should put glue on both sides. Press the boards down until the glue is fully incorporated. Before moving onto the next step, make sure the glue has dried completely.
After you have glued your boards, drill holes where you want to insert screws. Depending on what type screw you choose, the size of these holes will depend on how big they are. For example, if your screw is a 1/2-inch wooden screw, drill a hole that is at minimum 3/4 inches deep.
Once you have drilled the holes, the next step is to drive your screws through the joint into the board's backside. Do not hit the boards' front surfaces. It will ruin the finish. Don't drive the screws too far into the end. This will prevent splitting the wood's end grain.
You'll need to protect your completed project from the elements. You have two options: seal the whole furniture piece or just the top. It doesn't matter what method you use, you want something that will last many years. There are many options: oil-based varnishes; polyurethane; shellac; lacquer.
These products can usually be found at any home improvement store. Just make sure that you buy the right kind for the job. Some finishes are toxic and should not ever be used indoors. When handling certain finishes, wear protective gear.