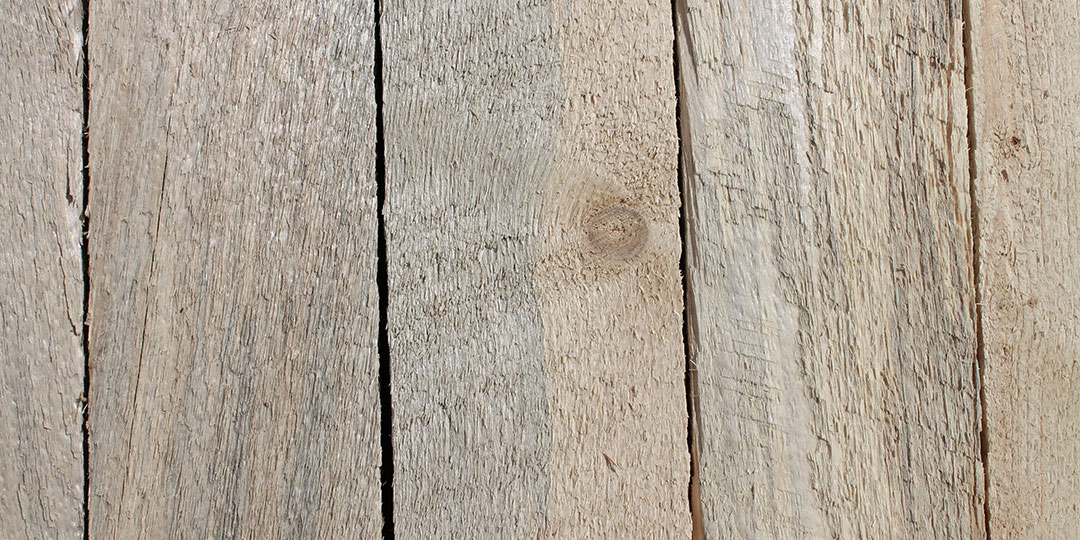
When glueing boards together, you will need glue. Glue can also be applied to one side of a joint. A roller makes it easy to apply a thin layer of glue. After the glue has been applied, let the boards cure for at most 24 hours before you move on to the next step. Any glue that is still oozing can be cleaned with damp cloth. The glue should be removed with either a chisel, or sandpaper. Be sure to give your curing time enough!
Glue boards from both sides
Gluing boards on both sides of the product will ensure it is flat and even. Be patient and don't rush the process. It is a complex task, so it should be done slowly. These are some tips that will ensure you have a successful outcome. Ensure that your board is flat and level and that it isn't buckling. Use the correct amount of adhesive and make sure you use the appropriate adhesive.
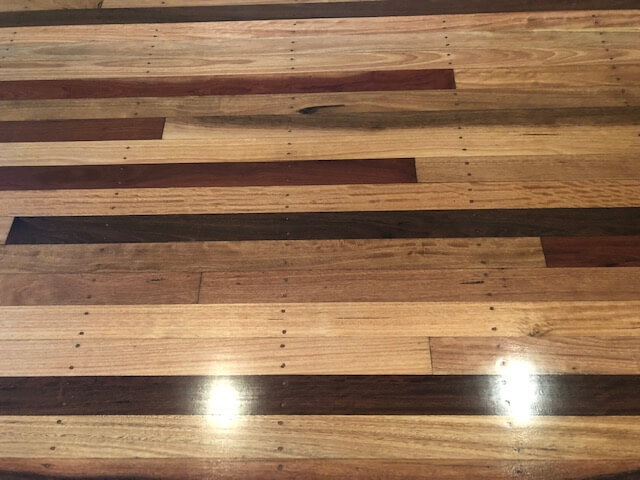
Apply glue to both the joints' edges
There are many advantages to glueing joints. It makes joints stronger and prevents them from cracking or breaking. Glue is not visible, so the edges are straight and smooth. Also, spread a generous amount glue evenly throughout the joint. Regularly using clamps along the joint will create an overlap of "cones for pressure". This method ensures a thin and strong glue line. Because they offer a lot of glue surface, lap joints are another option. For this type of joint, the following techniques are recommended.
Aboard thickness can be added
Each board should be at least 12 inch thick when you glue them together. You will end up with wood pieces that look like plywood if you don’t. However, multiple layers of wood will give your finished product a different look. It is important to consider the grain when glueing boards together. Poor grain matches can ruin the beauty and appeal of your project. Avoid this problem by purchasing boards from one log. Add a little more for waste. You can also use the stock that you have available.
Use a caul to glue boards
Gluing boards can be complicated. A caul will help you ensure a flat surface as well as a strong connection. A caul is simply an arbitrary piece of wood that you clamp parallel to the top edge of your table. Cauls should be made from hard wood and thicker in the vicinity of the glue seam. There are many ways you can use a glue board caul.
Avoidflex in cauls
For boards to be glued together it is essential to not allow the cauls to flex. This will prevent them from bowing. Cauls are curved and apply inward pressure. This can cause edge to edge boards to bow, even if they're symmetrical and the cauls are of the same stiffness. You can correct this by making sure the edges of your panels are square and glue them with a good adhesive.
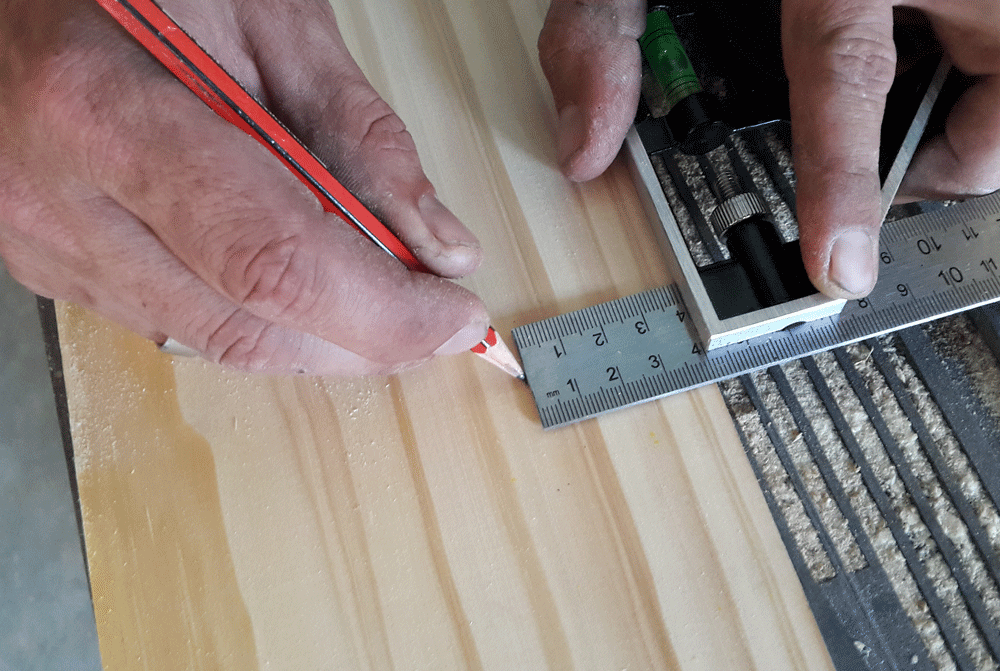
Creating mirror image grain patterns with edge-glued boards
Edge-glued boards are made by combining two pieces of wood with mirror image grain patterns. They are often used for veneers but can also made from solid boards. This involves resawing one wood piece and then joining it with glue. I will demonstrate a few methods to achieve this effect in this article. Read on to learn more.
FAQ
What woods are suitable for making furniture?
Woods are classified by their hardness. Softwoods are pine, cedar and cypress. Because they are resistant to rot, softwoods are often used as outdoor furniture. The hardwoods are oak, maple and mahogany. They're generally used indoors because they won't weather well outdoors.
How often should I buy new supplies?
Over time, you may need to replace your tools. Hand tools will need to be sharpened regularly. Power tools will require replacement parts every so often. To avoid buying too much at once, try to spread your purchases out over a few months.
Is it difficult to start my woodworking business?
It is not easy to start a woodworking business. You will need to adhere to many legal requirements. But, this doesn't mean you need to go through all of the trouble of setting up your business. Many people prefer to join existing companies. This allows you to join existing businesses and pay only membership fees.
How much do hobbyists need to invest in starting a business?
To start your own woodworking company, you will likely need capital to purchase the necessary tools and other supplies. You can start by purchasing a small table saw and drill press as well as a circular saw, circular saw, jigsaw and sanding machines. These items aren't very expensive, so you won't break the bank.
Does it take a genius to make woodworking work?
No. No. Woodworking isn't rocket science. Anyone can learn to use basic powertools and techniques to create beautiful work of art.
Statistics
- The U.S. Bureau of Labor Statistics (BLS) estimates that the number of jobs for woodworkers will decline by 4% between 2019 and 2029. (indeed.com)
- Average lumber prices rose about 600 percent between April 2020 and May 2021. (familyhandyman.com)
- Woodworkers on the lower end of that spectrum, the bottom 10% to be exact, make roughly $24,000 a year, while the top 10% makes $108,000. (zippia.com)
- The best-paid 10 percent make $76,000, while the lowest-paid 10 percent make $34,000. (zippia.com)
External Links
How To
How to join wood without using nails
Woodworking is a popular hobby. It's fun and relaxing because you can use your hands to make something useful from wood. Sometimes you may want to join two pieces together of wood without using nails. This article will help you to maintain the beauty of your woodwork projects.
You will first need to trim the edges of your wood pieces before joining them. Sharp corners can cause problems down the line. Now you can start gluing the boards together.
If you are working with hardwood, only one side should be glue. You should glue both sides if you are working with softwoods such as pine and cedar. After applying the glue, press the boards firmly until they are completely stuck together. Be sure to let the glue dry before you move on to the next step.
After you have glued your boards, drill holes where you want to insert screws. These holes will differ depending on the type and size of screw you are using. For example, if your screw is a 1/2-inch wooden screw, drill a hole that is at minimum 3/4 inches deep.
After drilling your holes, drive the screws into the board's backside. Don't hit the board's surface. You could damage the finish. Avoid hitting the screws' ends too often when driving screws. This will help prevent splitting of the end grain.
Now that your project is finished, you'll want to protect it from the elements. You have two options: seal the whole furniture piece or just the top. You'll want a product that lasts for many years. There are many options: oil-based varnishes; polyurethane; shellac; lacquer.
These products can generally be found in any home improvement shop. Make sure you get the right product for your job. Keep in mind that certain finishes can be toxic and should not be used indoors. Protective gear should always be worn when handling these finishes.