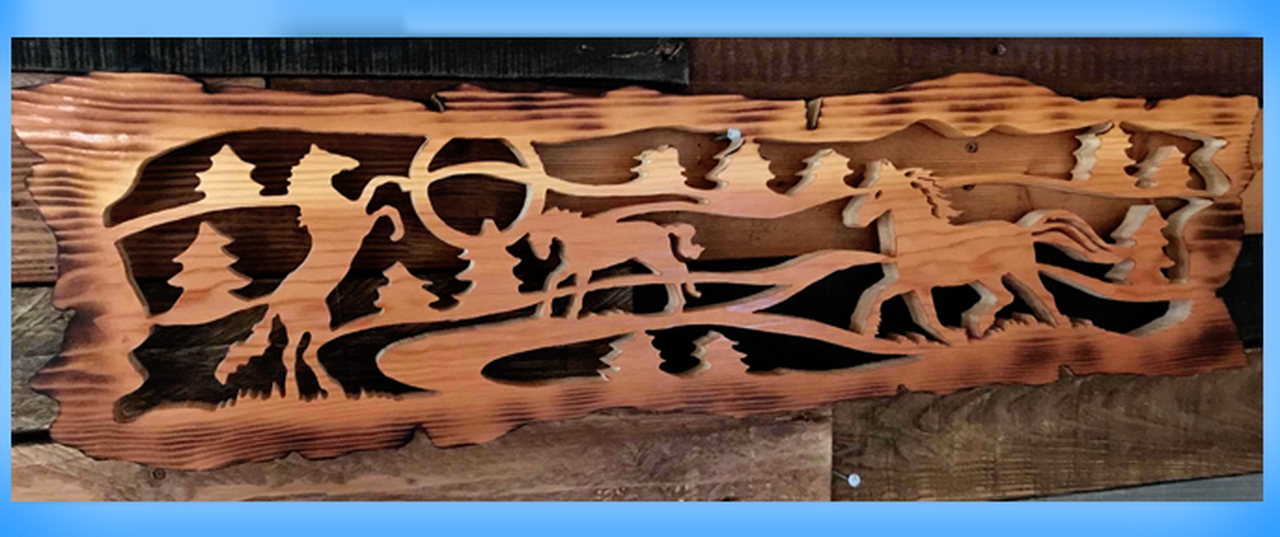
A scroll saw shadow box is an excellent way to display artwork or photographs. A shadow box of small size can give a sense of wonder. One simple scene can be created from seven layers 1/4" Baltic Birch plywood. It measures approximately 4 inches square and 1.75 inch thick. Small details add interest and awe to the finished piece. A shadow box that is larger would require more detail, and it would be more complicated. This is the scene from the inside of the shadow box.
Fox Classic fence
When you are building a scroll saw shadow box, one of the most important factors to consider is the type of fence you use. There are many options, including the T shape Shop Fox Classic fence, which is the original fence, as well as the T-slot accessory fence. Shop Fox Classic fences include a quick-release blade guard system and riving knife system. They are prewired to work on ordinary 120V 20A circuits and come with a 10" x 40T carbide-tipped blade.
Shop-Fox Classic fence is an option for your next project. This fence will last many years. The pattern options include the Five Layer Circle Art Scroll Saw Pattern (with a Duck Family Tray Scroll Saw Pattern), the Hanging OrganizerBox and the Four-Layer Jesus Cross. Each of these patterns includes a video tutorial to help you understand each step.
Fox Aluma - Classic fence
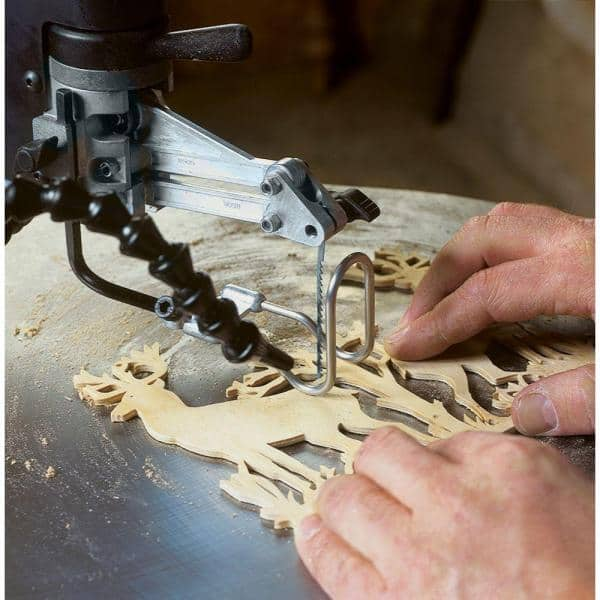
Shop Fox Aluma Classic fencing is a Tshaped accessory fence. It works with any shop-made Scroll Saw. The fence is very easy to set up, so you can easily cut even the largest panels. Prewired to work on an ordinary 120V-20A circuit, the fence has a 10-inch, 40T carbide tip blade.
Fox Original fence
Shop Fox Original fence for scrollsaws comes as an accessory. It features a T-shape blade guard, prewired knife guard, and riving system. It features a riving blade system and a 10"x40T carbide-tipped knife. If you're new to scroll sawing, you might want to start with a small project, such as a shadow box.
FAQ
How long does it take you to finish a piece?
It all depends upon the size of your piece of furniture. A smaller project like picture frames or boxes can be completed in a single day. Larger projects like dining tables and desks require several days. It takes time and effort to properly stain the wood.
Is it hard to start my own woodworking business?
It's not easy to start your own woodworking business. There are lots of legal requirements and regulations that you'll need to follow. You don't have to go through all that hassle of setting it up. Many people choose to join existing businesses. You only need to pay membership and tax fees.
What kind of wood should I use?
There are many wood types that are used in woodworking, including oak, maple and birch. Each wood type has its own characteristics which affect the final product's appearance and feel. For example, oak tends to be darker and harder than other woods. Birch is soft and lightweight, while mahogany is denser and heavier. You can also choose from solid wood or veneers. Veneers are thin sheets or wood that are glued together into one layer.
Which material would you recommend for woodworking lessons?
Start with softwood like pine, poplar and ash. When you feel confident with these two, move on towards hardwood.
Statistics
- In 2014, there were just over 237,000 jobs for all woodworkers, with other wood product manufacturing employing 23 percent; wood kitchen cabinets and countertop manufacturing employing 21 percent. (theartcareerproject.com)
- Overall employment of woodworkers is projected to grow 8 percent from 2020 to 2030, about as fast as the average for all occupations. (bls.gov)
- The best-paid 10 percent make $76,000, while the lowest-paid 10 percent make $34,000. (zippia.com)
- Woodworkers on the lower end of that spectrum, the bottom 10% to be exact, make roughly $24,000 a year, while the top 10% makes $108,000. (zippia.com)
External Links
How To
How to stain hardwood
Stain wood is a process that involves applying chemicals to the surface of wood, which changes its color. This chemical reaction causes the wood color to change from white and brownish red. Oak is the most commonly used wood for staining, but other woods can also be stained.
There are many ways to stain wood surfaces. You can mix the stain with a solvent, such as turpentine, and spray it onto the wood. Other methods use a solution of water and dye applied directly to the wood. You can mix stains into varnishes or paints to make them part of your finish coat.
Preparing the surface is the most important step in staining wooden surfaces. The wood must be thoroughly cleaned to remove all grease and dirt. Sanding smoothens any scratches or rough spots. Then you must decide what kind of stain you want to use. There are two main kinds of stains available: non-penetrating stains and penetrating. Penetrating and non-penetrating wood stains penetrate deeper than other types, making them perfect for dark colors like mahogany. The best non-penetrating colors are those that work with light colors like maple.
After choosing the type and application method you prefer, gather your tools. You can use a paintbrush to apply stains. This allows you spread the liquid evenly over the surface. To remove any stains left behind after painting, you will need some rags. If you are planning to mix your stain, ensure you have enough containers for each component.
After you have prepared your materials for staining, clean the area. Use warm water and soap to clean away dirt and dust. Use a dampened sponge and warm water to clean the entire piece. Be sure to get rid of all loose material, especially if staining is planned for darker wood.
Next, spray the stain. Start at one end of the piece of furniture and brush or spray the stain onto the wood. You should work slowly and carefully. Continue moving along the grain until you reach your opposite end. Be careful not to let the stain drip off the wood's edge. Let the stain dry completely before proceeding with the next steps.
A coat of clear polyurethane sealing agent is applied to protect the paint. Apply three coats polyurethane sealer. Allow the third coat, which should dry overnight, to dry before sanding.