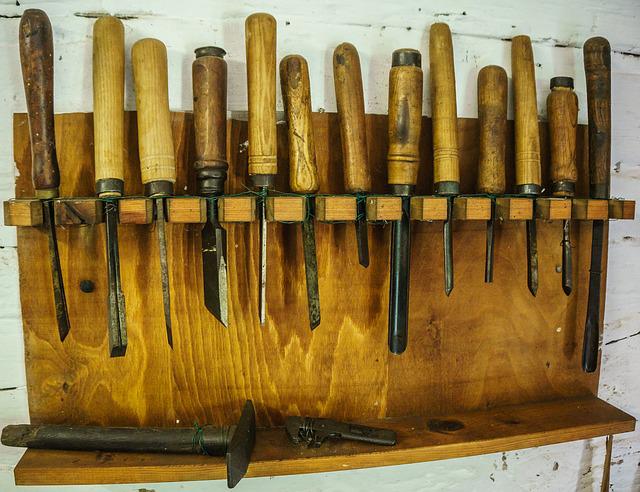
A good woodturning manual will give you the details on how to make a specific woodturning job. Some books concentrate on a single project, while others focus more on multiple projects. One of these books, Turning Custom Duck and Game Calls, is a great resource for woodworkers, outdoor enthusiasts, conservationists, and game call collectors. Ernie Conover is a writer who shares tips on starting your own woodturning workshop.
Mark Woodturning
Mark Woodturning books are great for beginners in woodturning. This book is a complete guide that will teach you everything about woodturning. This book contains demonstrations and detailed instructions for more than fifty projects. The book includes clear colour photos and working drawings that will help you complete each project. The book is simple and easy to read. The book is easy to follow and suitable for complete beginners.
The book Beginning Woodturning provides a great introduction to the basics. Throughout the book, Hayes teaches readers the basic skills of woodworking. The book covers fifty of the most common woods and provides practical information about them. Numerous woodturning projects can be found in the book. This book will also be helpful for anyone who is looking to buy lumber. A glossary of terms for wood is also included in this book. After they have learned the basics, this book will guide them through more advanced techniques.
Sam Maloof
Sam Maloof's books are a great way to learn the art of woodturning. His work is a great mix of technical mastery as well as mature artistic expression. His books set the standard for this genre. Other woodworkers have cited his works as models and have admired them. However, there's more to Sam Maloof's woodworking than meets the eye.
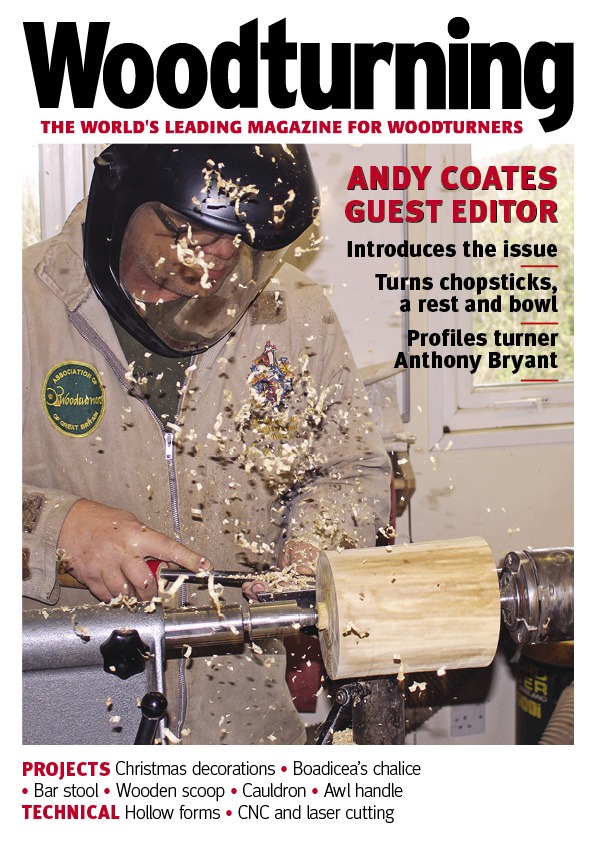
Born in Chino, California, Sam Maloof started working as a graphic artist before pursuing his passion for woodworking. Despite not receiving any formal training, he persevered and eventually became one the most prominent American custom furniture manufacturers. He has been elected to the American Craft Council as a Fellow, received many grants from Louis Comfort Tiffany Foundation, his work has been featured on numerous articles and books. His work has been so well-received that it is now part of the White House's permanent collection.
David Ellsworth
David Ellsworth's woodturning books are essential for any budding turner. They include step-by-step instructions with illustrated designs. This collection has everything a beginner in woodturning needs, including basic tools and expert tips. This book offers a wide range of projects, so there is something for everyone. This book offers expert advice on design, sharpening and tool making.
The Creative Woodturner, a book that is essential for any woodturner, whether they are a beginner or an intermediate one, teaches the fundamentals of woodturning and inspires readers not to be limited by their limitations. The book features hundreds of illustrations in color and detailed instructions for creating beautiful wood objects. This book makes it possible for beginners to improve their skills without having to sacrifice safety. There are also a number of supplementary videos that can teach the beginner everything he or she needs to know.
Carol Rix
Carol Rix has a wealth of books that will help you start woodturning as a hobby. Rix, an Australian native, has been turning timber since childhood. Before becoming a professional woodturner in 2001, Rix was a school teacher. In her work, she uses salvaged and recycled local timbers. She regularly writes articles for The Australian Woodworker and teaches woodturning classes. She is an excellent teacher and has a lot of knowledge to share.
In her books, Rix outlines all of the steps needed to get started and gives a detailed outline of what tools and techniques are necessary. The books also include practice projects and a gallery of ideas. Each step is illustrated in action shots. Rix covers everything you need to know, including advanced techniques and the basics. Every chapter is specifically designed to help you develop your skills. Rix also covers proper lathe safety, grain directions, reverse, jam chucking, sharpening tools, and shop-built Jigs.
Richard Raffan
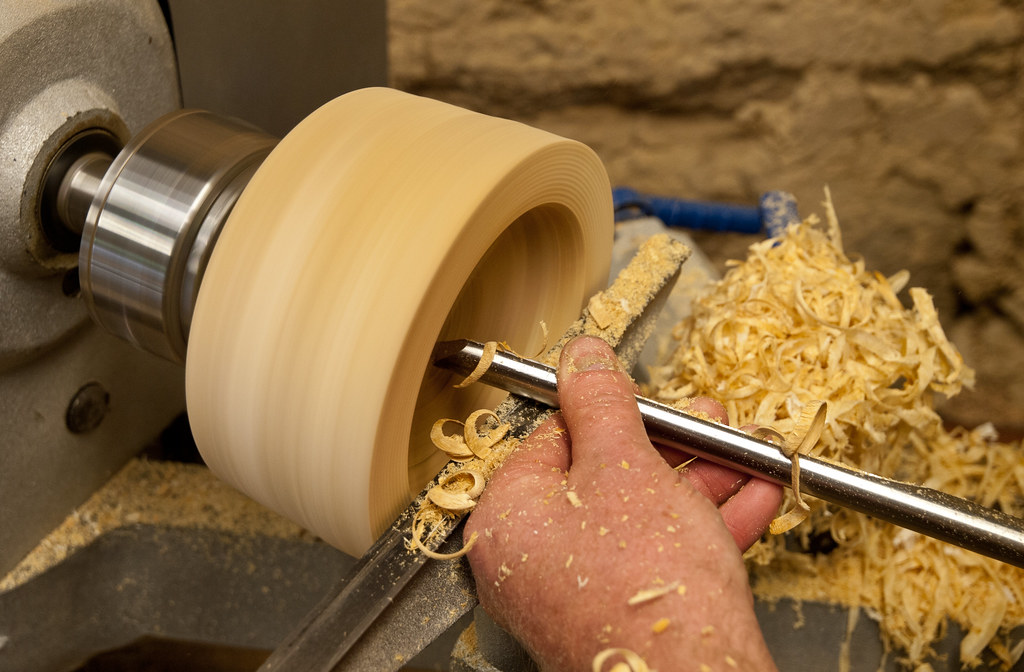
You may be looking to find a book that can help you with your turn projects. Richard Raffan's turn-guides are the best choice. The three-volume set comes with a beautiful slipcase. There are great tips for beginners here. You can also check out his Turning Project DVDs. These are great for learning how turn various items including hollow vessels like bowls.
Richard Raffan's All New Turning Projects includes both simple and complex projects as well as clear, easy-to-follow instructions. The book's layout and instructional style are similar to a woodworking course, with each chapter devoted to a specific technique. In addition, the photos and diagrams show how to complete each project, making it easy to understand and follow along. It is a great book for woodturners who are just starting out.
Mike Darlow
Mike Darlow has been recognized as one of the foremost experts on hand-woodturning. He has published 5 books on the subject. Design is his fifth. This book explores architectural applications of different column shapes and places wood turning's current fascination in historical context. Mike is also a superb teacher and has produced DVDs. You can also find a wealth of additional content from Mike. His website offers helpful information for beginners on how to turn woodturning tools into useful tools.
"Mike Darlow turned professionally for 16 year and has authored over 200 articles, seven books and seven books about the subject. His first books included The Practice of Woodturning. His work is displayed worldwide and he continues to exhibit and teach internationally. His books are a great resource for both novice and expert turners. Even if your craft is new, you'll find new ideas and techniques you didn't know were possible.
FAQ
What kind of wood should I use?
Oak, maple, cherry and mahogany are the most common wood types used for woodworking. Each type of wood has its own unique characteristics that can affect the final product's appearance. Oak, for example, tends be darker and more hard than other woods. Birch is lightweight and soft while mahogany is heavier and denser. You also have the option of solid wood or veneers. Veneers can be described as thin sheets of wood that have been glued together in one layer.
How long does a piece take to finish?
It depends on the type of wood you choose, the complexity of the design, and the amount of finishing you apply. Hardwoods, on the other hand, are more durable than softwoods. Hardwoods can also be more costly than softwoods. But they last longer and resist moisture better. The average time it takes to finish furniture is one week to three weeks.
How can you calculate woodworking pricing?
The most important thing to remember when calculating costs for any project is to keep them as low as possible. Make sure you're getting the best prices on materials. It's also worth taking into account all the other factors that may affect the cost of your projects, such as time, skill level, and experience. Our guide to the average household DIY task price will give you an idea of how much it costs to complete different types of woodwork projects.
What is the main difference between plywood or particle board?
Plywood is made of layers of wood that are pressed together under pressure. Plywood is available in a variety of thicknesses. It is often used to make cabinets or flooring. Particle board consists of sawdust mixed and resin. The resin is then compressed into large blocks. This board is commonly used in home improvement projects. Both boards can be cut easily and are both durable.
How can I organize my shop?
A designated place to store your tools is the first step towards keeping your workshop clean. Keep your tools away from dust and debris, so they stay sharp and ready to work. Pegboard hooks can be used to hang tools and accessories.
How much does a hobbyist need to invest in getting started?
You will need capital to purchase the tools and supplies you need to start your woodworking business. The best place to start is by buying a small drill press, circularsaw, circular saw or sanding machine. These items aren't very expensive, so you won't break the bank.
How can I tell what kind of wood I am working with?
Always check the label before purchasing wood. The label should provide information about the wood species, moisture content, and whether preservatives have been used.
Statistics
- Most woodworkers agree that lumber moisture needs to be under 10% for building furniture. (woodandshop.com)
- Overall employment of woodworkers is projected to grow 8 percent from 2020 to 2030, about as fast as the average for all occupations. (bls.gov)
- The best-paid 10 percent make $76,000, while the lowest-paid 10 percent make $34,000. (zippia.com)
- The U.S. Bureau of Labor Statistics (BLS) estimates that the number of jobs for woodworkers will decline by 4% between 2019 and 2029. (indeed.com)
External Links
How To
How to stain wooden surfaces
Staining wood can be described as a process where chemicals are applied to the wood surface. This causes the wood to take on a new color. This chemical reaction causes wood to turn from whiteish to brownish. Oak is the most commonly used wood for staining, but other woods can also be stained.
There are many ways to stain wood surfaces. You can mix the stain with a solvent, such as turpentine, and spray it onto the wood. Another method involves applying a solution of water to the wood. You can mix stains into varnishes or paints to make them part of your finish coat.
Preparing the surface for staining wood is the first step. Cleaning the wood thoroughly removes any dirt or grease that could interfere with applying the stain. Sanding smoothens any scratches or rough spots. Next, you need to decide which stain you want. There are two main types of stain: non-penetrating and penetrating. Penetrating stain penetrates deeper into wood than nonpenetrating, making them suitable for dark colors like mahogany. Non-penetrating stains work best with light colors like maple.
After choosing the type and application method you prefer, gather your tools. A paintbrush works well for applying stains because it allows you to spread the liquid evenly across the surface. You should also have some handy rags to wipe up excess stains after you finish painting. If you plan on mixing the stain yourself make sure that you have enough containers to hold the different components.
Once you have prepared all your materials, it is time to clean the areas where you will stain the wood. Use warm water and soap to clean away dirt and dust. Use a dampened rag and clean water to wipe the furniture. Be sure to get rid of all loose material, especially if staining is planned for darker wood.
The stain should be applied next. Begin at one end and spray or brush the stain on the wood. Work slowly and carefully, moving back and forth along the grain of the wood until you reach the opposite end. Be careful not to let the stain drip off the wood's edge. Before proceeding to the next step, let the stain dry thoroughly.
To protect the painted surface, apply a coat of clear polyurethane sealant. Apply three coats with polyurethane. Allow the third coat to dry overnight before sanding the final coat.